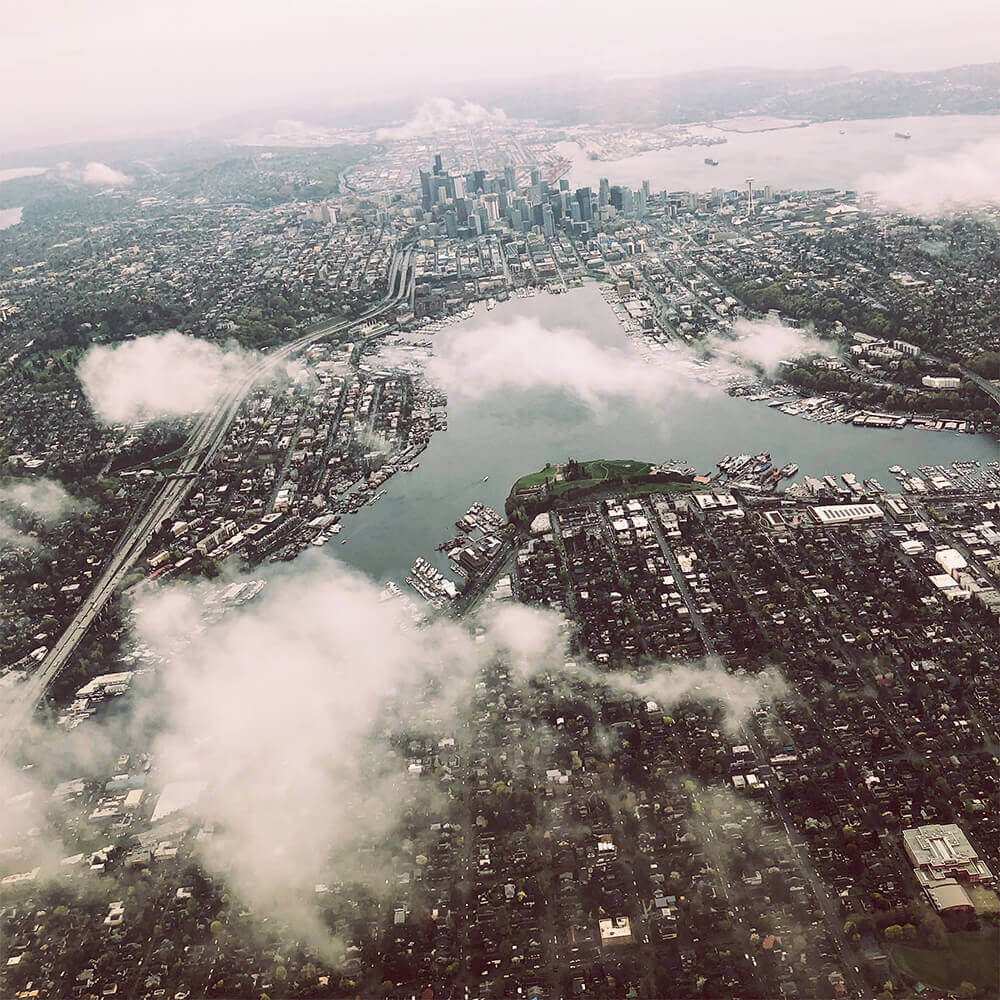
How Additive Help Create Stronger, More Durable Concrete and Much More
Did you know that you can tailor your concrete mix to suit your specific project needs?
Concrete suppliers mix in additives to batches of concrete to improve specific qualities of the final product. This includes accelerants or retardants to speed up or slow down the concrete’s setting time. Additives help to improve workability, strength, and quality.
Researchers are interested in the role additives play in creating better, more versatile concrete products on a molecular level. This could lead to tailoring concrete products to changing climates and environmental conditions, creating incredibly versatile and eco-friendly concrete that offers a wealth of benefits for construction companies and the finished products they create.
We’re taking a closer look at some of the ways additives help create better concrete products – and what that might mean for concrete of the future.
What Researchers Are Looking For
Two of the biggest challenges of concrete production are durability and sustainability. Researchers are always looking for news way to produce concrete that improves on these qualities.
Using local materials is an obvious solution to help offset the greenhouse gas emissions present during the production process but poses challenges in and of itself. In some cases, durability comes at the cost of sourcing materials elsewhere.
Additives help make “going local” a viable option and can improve on pre-existing mixes in some cases.
Furthermore, the use of sustainable, durable materials with a longer design life means less reliance on concrete production to replace structures in the future.
Researchers have analyzed the individual atoms in concrete that contribute to strength and durability, using this information to develop a computer model that simulates the behaviour of individual atoms, forming molecular building blocks in hardening material.
This research aims to find ways to create concrete products that are strong enough to withstand the increasing pressures of environmental conditions, such as earthquakes and floods, which place stress on concrete buildings and infrastructure.
Researchers are specifically examining how additives (such as volcanic ash from various regions and refinery slag) mixed into cement improve the cohesive and frictional forces of groups of atoms. The effect of these local additives on concrete mixtures could make concrete mixes better suited to specific regions for a more sustainable product.
Common Admixtures
Most concrete mixes today contain chemical additives, also known as admixtures. These help speed up concrete construction projects by making concrete easier to pour and work with. As a result, this increases productivity and cuts costs.
Admixtures also increase the strength and durability of concrete, reduce the amount of water needed in the mix, and speed up or slow down the setting time.
Local suppliers frequently use specific admixtures in your concrete mix based on your concrete project needs.
Let’s take a closer look at five common existing admixtures used in concrete mixes today:
1. Retarding Admixtures
Retarding admixtures slow down the setting rate of concrete by delaying the chemical reaction that starts the setting process. This makes concrete more workable during placement in hot weather.
These admixtures are necessary in hot weather since the heat can increase the concrete’s setting time.
When heat makes concrete harden faster, the concrete’s workability decreases, making placing and finishing the concrete difficult.
2. Accelerating Admixtures
Accelerating admixtures speed up the rate of early strength development in concrete.
This reduces the time needed for proper curing and protection, meaning finishing operations can start earlier.
Accelerating admixtures are especially useful in cold weather since the cold reduces the rate of setting.
3. Air-Entrainment Admixtures
Air-entrainment admixtures increase the durability of concrete during the freeze-thaw cycle. It also increases concrete’s workability and reduces bleeding and segregation.
These mixtures place microscopic air bubbles into the concrete, which prevents cracking from stresses such as water expanding in freezing temperatures.
4. Water-Reducing Admixtures
Water-reducing admixtures reduce the amount of water content required for a concrete mixture by 5 to 10 percent.
Concrete with this admixture will have a lower water-cement ratio, needing less water to reach the desired slump.
This makes it possible to produce higher-strength concrete without increasing the amount of cement used in the concrete. Less reliance on cement is more affordable and sustainable. Lower cement content reduces CO2 emissions and energy use per volume of concrete.
Water-reducing admixtures improve concrete properties, make it easier to place concrete in difficult conditions, and are more stable across a wide range of temperatures.
5. Superplasticizers
Superplasticizers—also known as plasticizers and high-range water reducers (HRWR)—reduce water content by 12 to 30 percent.
Superplasticizers create high-slump flowing concrete out of concrete mixes with low-to-normal slump and water-cement ratios. This increases the workability of concrete, making it highly fluid and easy to place with little to no compaction.
Superplasticizers only increase concrete workability for 30 to 60 minutes, so concrete contractors will usually add superplasticizers to the mixture at the job site instead of at the concrete plant.
What This Could Mean for Concrete In The Future
Concrete additives improve workability and durability. And with the current research into the role additives play on a molecular level, concrete additives could eventually be tailored to changing climates and environmental conditions, such as withstanding natural disasters.
The use of concrete additives sourced locally, such as recycled fly ash, will reduce the carbon footprint of concrete production, especially if this means less reliance on cement for the production of concrete.
Better quality concrete tailored to withstand environment stressors will last longer, requiring less concrete production in the long run. This will result in fewer CO2 emissions and, with any luck, a greener future.