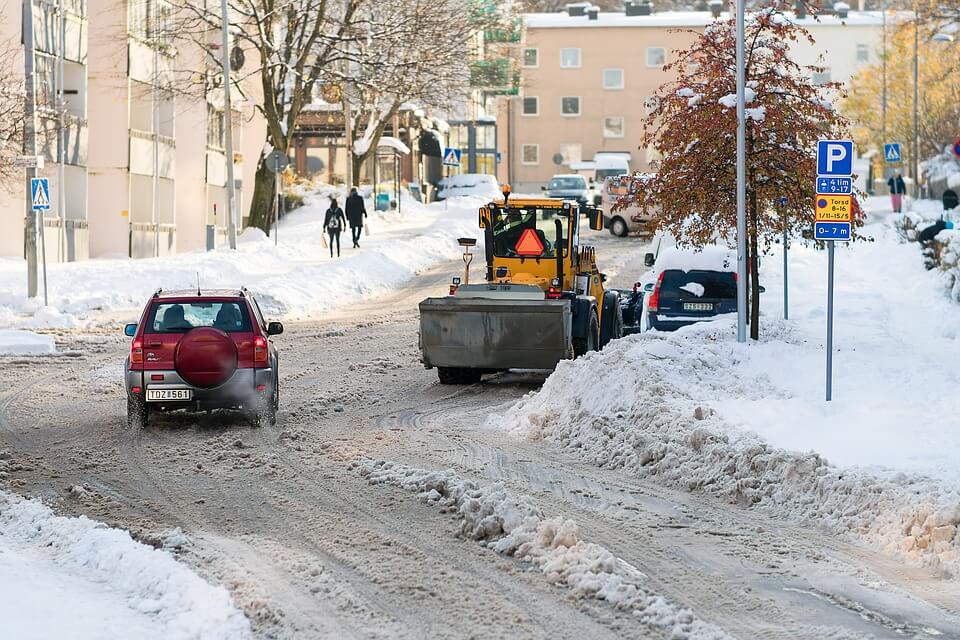
Researchers Have Found a Method to Create Concrete and Pavement that Melts Snow
With winter just around the corner, snow plows, salt trucks, and hazardous driving conditions will soon be a regular occurrence on our roads. While we all dread the harsh winter conditions, we’ve come to accept this unpleasant weather as a part of Canadian life. But imagine if the roads cleared themselves of snow and ice on their own—instead of waiting for the snow plow to come by, the snow would melt with the help of heated pavement.
Thankfully, researchers have found a way to create snow-melting concrete. By mixing paraffin wax with concrete products, this new concrete warms and melts the snow and ice when the temperature drops. This new concrete mix can melt snow more efficiently than salt and is also more environmentally friendly.
The copious amounts of salt used on roads every winter contribute to the fast deterioration of pavement and vehicles while depositing huge amounts of salt in the environment. Salt is also costly to use and distribute on roads all winter long. And the cost of repairs needed from salt damage to concrete can add up.
So a cost-effective, environmentally-friendly solution to snow removal is a must for areas hit hard by winter.
How It Works
Here’s how two innovative snow-melting concrete solutions work to melt snow and ice on concrete pavement in winter:
Using Phase Change Materials
This snow-melting concrete relies on the phase change material quality of paraffin oil. Phase change materials store heat and emit heat during the winter. When the paraffin oil freezes from liquid to solid, it releases thermal energy (heat).
Concrete treated with paraffin oil melts snow by warming the concrete during the phase change process of freezing. During product testing, researchers found that treated concrete melts snow within a day, while untreated concrete leaves snow intact for the most part.
Using Electricity-Conducting Materials
Another type of snow-melting concrete product uses conductive materials in the concrete mix. These electricity-conducting materials include steel shavings and “coke breeze,” which is a carbon by-product of coal mining.
Steel rods are then embedded in the conductive concrete slab. These rods are attached to electrodes that are connected to a 120-volt AC power source. When the power source is on, the steel rods heat up, and that heat energy spreads throughout the conductive concrete.
Conductive concrete heats up more evenly and efficiently than regular concrete with an embedded heating source like underground coils since the conducting materials are spread throughout the concrete mix, keeping the heat dispersed evenly. So the entire concrete slab heats up, and there are no cold spots.
Affordable Solutions
Use of by-products from the coal and steel industries can help significantly reduce the costs of the electricity-conducting concrete mix, while also being an environmentally-friendly option since it’s recycling products instead of sending waste to landfills.
Paraffin wax is also a low-cost material, so mixing it with concrete products could be a cost-effective and convenient way to keep roads clear during the winter. This would also reduce the amount of salt deposited on roads and in the surrounding natural environment.
Both the paraffin snow-melting discovery and the innovative conductive concrete are likely to be time-savers at airports in cold climates. Often, airports face lengthy delays and cancellations during the winter months, which cost airlines millions of dollars each year.
Airports must also constantly stay on top of keeping runways and tarmacs clear of ice and snow. Airport runway pavement that melts ice and snow with the help of paraffin wax or electricity could result in fewer delays and cancellations in the winter, making airlines and airport operations more efficient, saving significant costs and keeping air travellers happy.
Caring For Concrete In Winter
Until these innovative snow-melting concrete products become widely used where winter weather strikes, we have to use traditional snow removal and ice-melting methods on our roads and concrete pavement.
Unfortunately, the freeze-thaw cycle of winter, along with de-icing chemicals (such as salt), and the abrasion of shovels and snow plows can all take a toll on the quality of concrete. And if there is any damage to concrete before winter arrives, this damage will only get worse during the long winter.
So to care for your concrete in winter, and prevent damage to your concrete, such as scaling, spalling, and cracking, make sure to use quality concrete products that are mixed, poured, cured, and sealed properly.
Air-entrainment, water content, and additives can all help a concrete mix withstand the harsh winter weather. And sealers can keep water from saturating concrete, freezing, expanding, and ultimately cracking concrete.
During winter, follow these care tips to prevent damage to your concrete:
- Use a plastic-blade snow shovel instead of a metal shovel.
- Avoid the use of snow blowers on concrete. If you must use one, keep it well maintained, beware of the potential damage it can cause to your concrete, and use it sparingly.
- Use clean sand (not beach sand) or clay kitty litter instead of de-icing chemicals and rock salt on walkways, especially if the concrete is new (less than two years old).
- Never use de-icing products that have ammonium nitrate or ammonium sulfate. These chemicals, along with urea, are also found in common garden fertilizers, and can rapidly disintegrate concrete.
- Don’t clear off snow from concrete that isn’t in use—such as your concrete patio or pool deck. Snow actually acts as an insulating blanket on concrete, protecting it from the damage of the freeze-thaw cycle in winter.
Common Maintenance Needs
Once the snow has melted, and winter is finally over, you will need to inspect your concrete for damage that may have occurred over the winter, such as cracking, spalling, and scaling. It’s important to address any maintenance issues with your concrete to prevent this damage from worsening over time. Common maintenance includes patching and filling any cracks, and resurfacing spalling or scaling concrete.
Re-sealing concrete is another important step to protect your concrete from stains, scratches, or water saturation. If your concrete is in need of re-sealing, spring is the time to do this job. You should avoid re-sealing concrete later in the year, especially if you are using a film-forming sealer to maintain colour on decorative and stamped concrete. If applied too thick, these sealers retain moisture within the concrete slab, which is harmless in spring and summer, but harmful once the temperature drops below freezing in late fall and winter.
Penetrating sealers prevent moisture penetration, extending the life of concrete slabs. So choose a sealer based on the type of concrete you have. For example, you can extend the life of your plain concrete driveway or walkway by applying a penetrating sealer every 5 to 10 years. This sealer will prevent water penetration and cracking from the freeze-thaw cycle of winter.
And for any decorative and stamped concrete, such as on patios, pool decks, steps, walkways, or porches, apply a film-forming sealer every 3 to 5 years. These sealers also protect concrete from winter damage but provide little protection if the sealer wears too thin.
So keep an eye on your sealer over time. If you notice it’s wearing thin, or if water no longer beads on top of your penetrating sealer, then it’s time for a re-seal.
Snow-Free Roads Could Be Closer Than You Think
While we still have a ways to go before snow-melting concrete is the norm, there are ways to take care of your concrete and prevent it from winter damage in the meantime.
Researchers still need to test how paraffin wax affects concrete in the long run. Concrete durability, stability, and skid-resistance can’t be compromised. And they also need to make conductive concrete a more affordable option.
But if cleared for use on roads, these innovative concrete products will have a positive impact on road safety in the winter, while saving millions of dollars on salting roads, repairing damaged concrete, and reducing the harmful amounts of salt entering the environment each year.